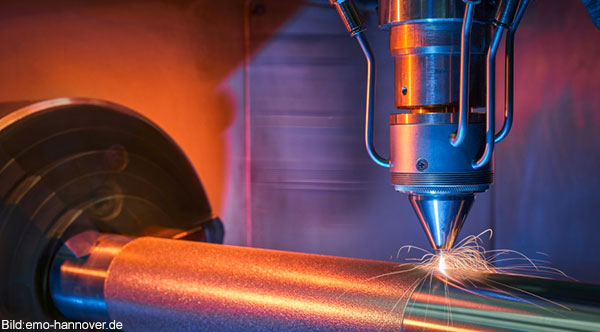
11.12.2018
Rasant und umweltfreundlich beschichten
EMO Hannover 2019 – Neues Verfahren zeigt additive Fertigungstechnologie auf einer Werkzeugmaschine
Das neue Verfahren für extremes Hochgeschwindigkeits-Laserauftragschweißen (Ehla) ist eine echte Success-Story: intensive Verfahrensentwicklung in Aachen seit 2012, konsequente Realisierung und Erprobung der Systemtechnik in den Niederlanden und dann die industrielle Umsetzung in China. Und am 21. September 2018 hat das am Aachener Fraunhofer-Institut für Lasertechnik ILT und am Lehrstuhl für Digital Additive Production DAP der RWTH Aachen University entwickelte Verfahren in Ditzingen nun auch noch den Berthold Leibinger Innovationspreis erhalten. Der Preis wird seit 2000 alle zwei Jahre für herausragende Forschungs- und Entwicklungsarbeiten zur Anwendung oder Erzeugung von Laserlicht verliehen.
Die Bauanleitung für die weltweit wohl schnellste Anlage zum Laserbeschichten ist an und für sich sehr einfach: Man nehme eine CNC-Drehmaschine, installiere eine Laserstrahlquelle, einen Bearbeitungskopf und ein Pulverzufuhrsystem – fertig. Dieser clevere Einsatz additiver Fertigungstechnologie wird auf der EMO Hannover 2019 der Öffentlichkeit präsentiert.
Das neue Verfahren löst ein Problem, das besonders Hersteller von stark beanspruchten Bauteilen aus Metall betrifft. Sie müssen Bauteile beschichten, damit sie nicht korrodieren oder verschleißen. Extrem hoch sind zum Beispiel die Ansprüche an die Beschichtungen für meterlange Offshore-Zylinder, die im Meer wegen der salzigen Umgebung schnell rosten und verschleißen. Allerdings warten die üblichen Beschichtungsverfahren – das Hartverchromen, das thermische Spritzen und das Auftragschweißen – mit Nachteilen auf. Auch das Laserauftragschweißen konnte sich bislang in diesem Bereich nur vereinzelt durchsetzen.
Alternative zum Hartverchromen
Das gängigste Verfahren für den Verschleiß- und Korrosionsschutz war bisher die Hartverchromung mit Chrom(VI), das aber wegen seiner umweltschädigenden Wirkung in die EU-Chemikalienverordnung EC 1907/2006 (REACH) aufgenommen wurde. Seit September 2017 darf es daher nur noch nach Autorisierung beziehungsweise besonderer Zulassung verwendet werden. Mit diesem Problem wurde die IHC Vremac Cylinders B.V. aus Apeldoorn (Niederlande) konfrontiert, die Hydraulikzylinder mit bis zu 10 m langen Kolbenstangen produziert. Diese kommen unter extrem harten Bedingungen in Baggern, Offshore-Anlagen, Tief-bau und in Schwermaschinen zum Einsatz.
„Wir suchten schon länger nach neuen Firmen, die duktile und härtere Schichten effektiv auftragen“, erklärt Andres Veldman, Manager Engineering bei IHC Vremac Cylinders. Für duktile Schichten eignen sich elektrolytische Verfahren und für harte Schichten kommt das Hochgeschwindigkeitsflammspritzen (HVOF) infrage. Aber auch den Laser nahm man in Apeldoorn ins Visier. Erste Untersuchungen im Jahr 2006 ergaben zwar, dass normales Laserauftragschweißen zu teuer und zu kompliziert ist. „Doch wir glaubten fest daran, dass diesem Verfahren die Zukunft gehört“, erinnert sich Veldman.
Laserbeschichten ermöglicht traumhafte Werte
Er hat sich nicht geirrt: Den Durchbruch verdankt das Verfahren maßgeblich einer Innovation bei der Verfahrensführung, die viel größere Beschichtungsgeschwindigkeiten ermöglicht. Der metallische Zusatzwerkstoff wird direkt im Laserstrahl geschmolzen und nicht erst im Schmelzbad. Die Folge: Ehla beschichtet mit einer Prozessgeschwindigkeit von bis zu 500 m/min. Üblich sind bisher 0,5 bis 2 m/min. Ehla ermöglicht außerdem viel dünnere Schichten aufzubringen. Waren bisher nur über 500 Mikrometer dicke Schichten möglich, so lassen sich nun 25 bis 250 Mikrometer dünne Schichten realisieren. Zudem werden die Schichten glatter, die Rauheit wurde auf ein Zehntel des für Laserauftragschweißen typischen Wertes reduziert.
Den Markterfolg verdanken die Aachener aber auch zwei mutigen niederländischen Pionieren. Auf der Suche nach einem Anlagenhersteller stießen die Wissenschaftler auf die noch junge Firma Hornet Laser Cladding B.V. aus Lexmond (Niederlande), zu deren Gründern Jelmer Brugman und Frank Rijsdijk sie seit vielen Jahren eine enge Verbindung haben. In ihrer Fabrik entstand 2014 die erste Ehla-Anlage. Dabei handelt es sich im Prinzip um einen „aufgerüsteten“ Drehautomaten. Den Hintergrund erläutert Thomas Schopphoven, Leiter des Teams „Produktivität und Systemtechnik“ in der Gruppe Laserauftragschweißen am Fraunhofer ILT: „Der Vorteil beim Beschichten von rotationssymmetrischen Bauteilen ist, dass sich die erforderlichen Komponenten – also Laserstrahlquelle, Ehla-Bearbeitungskopf und Pulverzufuhrsystem – gut integrieren und steuerungstechnisch anbinden lassen.“
Verfahren bereits international im Einsatz
Das Zusammenspiel von Fraunhofer ILT und Hornet überzeugte IHC in Apel-doorn. „Auf der Basis eines Drehmaschinentyps, die sich bei uns bereits in Apeldoorn im Einsatz befand, entstand eine völlig neue Anlage“, erinnert sich Veldman. „Es war eine clevere Idee, denn notfalls hätten wir sie – so unser Plan B – auch als Drehbank nutzen können. Beschaffung und Umbau der Drehmaschine zur rund 14 Meter langen Ehla-Anlage und Aufbau sowie Inbetriebnahme dauerten nur knapp sechs Monate.“
Die Niederländer befinden sich nun bereits in der Serienproduktion. Nach mehreren abgeschlossenen Projekten steht für Veldman fest, dass das Verfahren derzeit noch etwa so viel wie das thermische Spritzen kostet. Preiswerter wird es – so seine Einschätzung – nach der Optimierung der Endbearbeitungsprozesse. Kunden etwa aus dem Offshore-Bereich konnten die Apeldoorner allerdings schon jetzt von der neuen Schicht überzeugen. Dazu ließ das Unternehmen Ehla von der Risikomanagement-Organisation Lloyd’s Register (LR) nach DIN EN ISO 156147 zertifizieren. Veldman: „Die Fachleute waren anfangs sehr skeptisch, weil wir nur 200 Mikrometer dünne Schichten im Labor prüfen ließen, die dann noch auf 150 bis 100 Mikrometer heruntergeschliffen wurden. Damit wollten wir sichergehen, dass die Schichten auch nach Verschleiß noch guten Korrosionsschutz bieten.“ Die Experten von IHC wussten dabei, was sie taten. Seit 2015 hat das Unternehmen einige hundert Hydraulikzylinder für den weltweiten Offshore-Einsatz mit Längen von bis zu 10 m und Durchmessern von bis zu 500 mm mit verschleiß- und korrosionsbeständigen Legierungen für höchste Ansprüche beschichtet.
Auf die Vielzahl an möglichen Anwendungen setzt auch die Trumpf Laser- und Systemtechnik GmbH aus Ditzingen, die mittlerweile Laseranlagen inklusive Ehla-Verfahren für unterschiedliche Bauteilgrößen anbietet. Die umweltfreundliche und schnelle Technik überzeugt aber auch außerhalb Europas. Neuerdings setzen auch chinesische Anwender auf das Verfahren. So erläutert Chen Hong, Geschäftsführer der ACunity GmbH aus Aachen, einem Spin-off des Fraunhofer ILT: „Der Bedarf für das Ehla-Verfahren ist sehr hoch, denn China will in den nächsten zwei Jahren das Hartverchromen nach europäischem Vorbild reglementieren.“ 2017 ging das Spin-off daher eine strategische Kooperation mit der China Academy of Machinery Science and Technology Group Co., Ltd. (CAM) in Peking ein und lieferte eine 5-Achs-Anlage mit einer vom Fraunhofer ILT angepassten Ehla-Düsentechnologie. Nach den erfolgreichen Einsätzen bei CAM in Peking orderte das Unternehmen Hebei Jingye Additive Manufacturing Technology Co. Ltd. zwei Anlagen zur Außenbeschichtung von bis zu fünf Meter langen Offshore-Hydraulikzylindern mit einem maximalen Durchmesser von einem Meter sowie eine weitere Anlage zur Innenbeschichtung. Nach dem ersten Erfolg des Ehla-Verfahrens in China ist Geschäftsführer Hong optimistisch, dass demnächst Aufträge aus der Offshore-Branche über fünf bis zehn Anlagen folgen. Mit den nächsten Aufträgen soll sich auch die Produktionsweise ändern. Handelte es sich bisher in erster Linie um maßgeschneiderte Sondermaschinen, soll nun ein Modulbaukasten für kleine, mittlere bis hin zu sehr großen Anlagen entstehen.
Das Verfahren läuft anderen den Rang ab
Im Kommen sind außer Ehla auch andere Verfahren – wie das laserbasierte Auftragen von Nanostrukturen (Projekt Laser-4-Fun, www.laser4fun.eu ), oder auch Weiterentwicklungen von klassischen Verfahren wie dem Wolfram-Inertgas- oder dem Plasma-Pulver-Auftragschweißen (PTA). „Weltweit existiert außer Ehla bisher aber kein anderes flexibles, ressourceneffizientes und gleichzeitig wirtschaftliches Beschichtungsverfahren für das Auftragen hochqualitativer, schmelzmetallurgisch angebundener, dünner Schichten“, betont Schopphoven. „Wegen der formschlüssigen Verbindung gibt es hier deutliche Vorteile gegenüber Schichten, die mit thermischem Spritzen oder elektrochemischen Verfahren aufgetragen werden – denn dort ist die Schichthaftung nur sehr begrenzt.“
Bild & Text: emo-hannover.de